Understanding Injection Molded Plastic Manufacturers
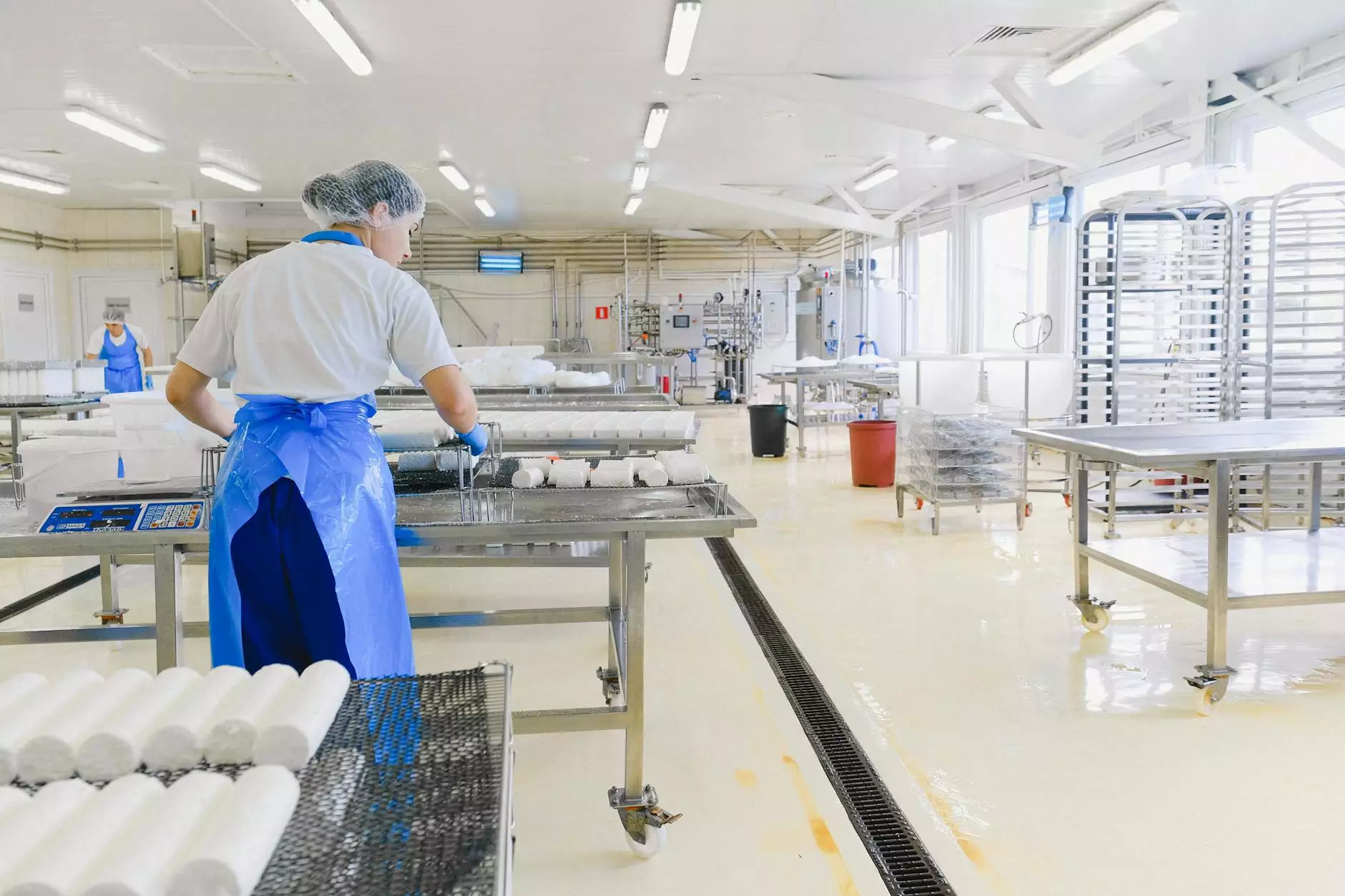
In today's rapidly evolving industrial landscape, injection molded plastic manufacturers serve a crucial role in the production of numerous products that we use daily. From household items to complex automotive parts, these manufacturers employ advanced techniques and innovative technologies to deliver high-quality plastic components. In this article, we will explore the intricate world of injection molding, the benefits of this manufacturing process, and why choosing the right manufacturer, like Deep Mould, is essential for your business success.
The Injection Molding Process Explained
To understand the importance of injection molded plastic manufacturers, it's essential to grasp the mechanics of the injection molding process. Here’s a detailed breakdown:
1. Material Selection
Injection molding begins with selecting the right material. Typically, manufacturers opt for thermoplastics like:
- Polyethylene (PE)
- Polypropylene (PP)
- Polyvinyl Chloride (PVC)
- Acrylonitrile Butadiene Styrene (ABS)
- Polycarbonate (PC)
Each material possesses unique characteristics that determine its suitability for particular applications.
2. Designing the Mold
The mold design is a critical step. It involves creating a blueprint that reflects the final product's specifications. Factors such as:
- Product dimensions
- Wall thickness
- Draft angles
- Cooling channels
must be considered to ensure optimal molding performance and ease of part removal.
3. The Injection Molding Machine
The next step is the use of an injection molding machine. This machine heats the selected plastic pellets until they become molten and then injects this liquid plastic into the prepared mold under high pressure. The process can be divided into:
- Melting: Heating the pellets to a temperature suitable for injection.
- Injection: Injecting the molten plastic into the mold.
- Cooling: Allowing the plastic to cool and solidify in the mold.
- Ejection: Removing the finished part from the mold.
4. Quality Control
Once produced, the parts undergo rigorous quality control measures to ensure adherence to industry standards and specifications. This step is vital to avoid defects and maintain the reputation of the manufacturer.
Benefits of Injection Molding
The many advantages of choosing injection molded plastic manufacturing are a significant reason behind its popularity in various industries. Here are some of the key benefits:
1. High Efficiency
Injection molding is remarkably efficient, capable of producing large volumes of parts in a short period. This efficiency translates into lower costs per unit, making it an ideal choice for mass production.
2. Design Flexibility
Mold design allows for a wide range of shapes and sizes, enabling manufacturers to explore innovative product designs without significant additional costs.
3. Material Versatility
With a vast array of thermoplastics and additives available, manufacturers can customize materials for specific applications, enhancing product performance.
4. Consistency and Quality
Injection molded parts offer excellent dimensional accuracy and uniformity. The automated nature of the process minimizes human error, ensuring each part meets the required standards.
5. Reduced Waste
This manufacturing process generates minimal waste compared to traditional machining methods. The excess material can often be recycled, contributing to sustainability in manufacturing.
Applications of Injection Molded Plastics
Injection molded plastic components are ubiquitous across many sectors. Here are some prominent applications:
1. Automotive Industry
In the automotive sector, injection molded parts such as dashboards, door panels, and even under-the-hood components are commonplace due to their durability and lightweight properties.
2. Consumer Products
Everyday items such as containers, toys, and household appliances often come from injection molding processes, thanks to their ability to create complex shapes efficiently.
3. Medical Devices
Injection molded plastics play a critical role in producing medical devices, ensuring sterility and precision in the manufacturing of syringes, pill bottles, and surgical instruments.
4. Electronics
In the electronics industry, housings for various devices like smartphones and laptops are frequently manufactured through injection molding, combining aesthetic appeal with functionality.
Choosing the Right Injection Molded Plastic Manufacturer
With numerous injection molded plastic manufacturers in the market, selecting the right partner is crucial for achieving the desired quality and performance. Here are some tips to guide your decision:
1. Experience and Expertise
Look for manufacturers with a proven track record and extensive experience in the industry. Their expertise can be invaluable in navigating complexities during production.
2. Advanced Technology
Choose a manufacturer that invests in the latest molding technologies and practices. State-of-the-art equipment ensures higher precision and quality in the final products.
3. Quality Assurance Practices
It is essential to ensure that the manufacturer has rigorous quality control measures in place. Credentials, certifications, and a strong commitment to quality will reflect positively on their reliability.
4. Customer Support
Partnering with a manufacturer that offers excellent customer service can enhance your overall experience. Responsive communication and support can be vital, especially for addressing any concerns or modifications needed during production.
5. Sustainability Practices
In today's market, sustainability is increasingly critical. Choose a manufacturer that prioritizes eco-friendly practices, such as recycling and using sustainable materials in their processes.
Deep Mould: Your Go-To Injection Molded Plastic Manufacturer
At Deep Mould, we pride ourselves on being leaders in the field of injection molded plastic manufacturing. Our commitment to quality, innovation, and customer satisfaction sets us apart. Here’s what we bring to the table:
1. Custom Solutions
We specialize in creating customized solutions tailored to meet the unique needs of our clients. Our advanced capabilities ensure that we can handle projects of any complexity.
2. State-of-the-Art Technology
At Deep Mould, we invest in cutting-edge technology and equipment, allowing us to maintain high efficiency and precision across all our manufacturing processes.
3. Comprehensive Services
We offer a full suite of services, from design and prototyping to mass production and quality assurance, making us a one-stop solution for all your injection molding needs.
4. Experienced Team
Our team of professionals has extensive experience in the industry, ensuring that you receive top-notch guidance and support throughout your project.
5. Commitment to Sustainability
We are dedicated to implementing sustainable practices within our processes, ensuring minimal environmental impact while delivering outstanding products.
Conclusion
In conclusion, the role of injection molded plastic manufacturers cannot be overstated. With their ability to produce high-quality, consistent, and cost-effective products, they are integral to many industries. By partnering with a reputable manufacturer like Deep Mould, you can ensure that your requirements are met with excellence and efficiency. Whether you are in the automotive, medical, or consumer products space, embracing the benefits of injection molding can propel your business to new heights. Reach out to us today to discuss how we can assist with your manufacturing needs!